QUALITY & PRODUCTION MANAGEMENT
品質と生産管理
QUALITY CONTROL
品質管理
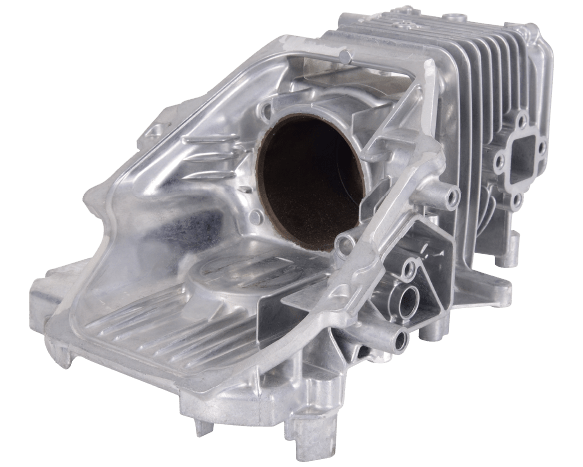
自工程完結+αの徹底した品質管理システム
ダイカスト金型をはじめとする私たちの金属加工技術は、
お客様が高品質な製品を継続的に世に送り出すための母胎となるものです。
私たちには、ものづくりの根幹を支えている責任と自負と製品への愛情があり、
常に最良のものを提供していく努力を惜しみません。